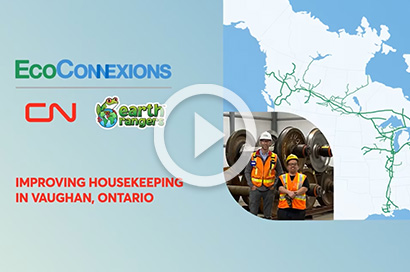
Some workspaces at the MacMillan Locomotive Reliability Center (LRC) in Vaughan, ON, were getting clogged with heavy mechanical equipment – important parts that shop employees need to maintain and repair locomotives. At the same time, this equipment often got in the way and bogged down work, as employees had to walk back and forth across the shop to get materials to do their jobs.
This situation was several years in the making, and that’s why Inventory Maintainer-Lead Hand James Harkin and LRC Senior Manager Jeff Willett made up their minds to do something for the safety and effectiveness of their team and shop.
Together, they researched options. The shop has a separate storage building, but it doesn’t have a concrete foundation, making it unusable for equipment that needs to be protected from ground moisture and temperature extremes. There weren’t available spaces inside the shop either.
James and Jeff put their heads together to identify an insulated fiberglass dome, which could be custom-built to meet infrastructure requirements for secure storage. They also needed to find a place to put the 26-by-146-foot dome, so they proposed removing about 30 feet of an unused storage track near the shop.
James and Jeff focused on safety, housekeeping and asset utilization benefits to receive project approval. The local Health and Safety Committee also had identified their storage issue as an ongoing opportunity.
After contract and delivery-related delays during the pandemic, James and Jeff’s persistence and patience as EcoChampions finally paid off when the dome was installed in Spring 2022. In between his other responsibilities, James used a forklift to carefully relocate their equipment into the new storage space. “I’m really proud of the accomplishment and that we got this done,” said James. “It’s a big win for the team.”
Adds Jeff: “There was a shock factor – in a good way – that this project finally happened! It’s always positive when a large project gets completed and everyone can see the positive result and know ideas like this are possible.”
The dome now houses a variety of traction motors, gear cases, wheels, oils and lubricants – all neatly organized and easy to access. It also allowed the team to clean up other eyesores, including a 30-foot wheel rack and radiators that were collecting outside.
“There is less of a tripping hazard, and our people don’t take unnecessary risks in moving 20 things out of the way to get to something they need to do their jobs,” Jeff said. “Everyone is safer and more productive.”
In addition to helping the 225 shop employees, the storage dome has economic and environmental benefits as it expands the lifespan of mechanical equipment which reduces waste.
CN’s EcoConnexions Employee Engagement program – in partnership with Earth Rangers – drives sustainability across CN's network by empowering employees and their families to conserve energy, reduce waste, and improve housekeeping.
Visit our Delivering Responsibly section to learn more about sustainability at CN.
LEARN MORE